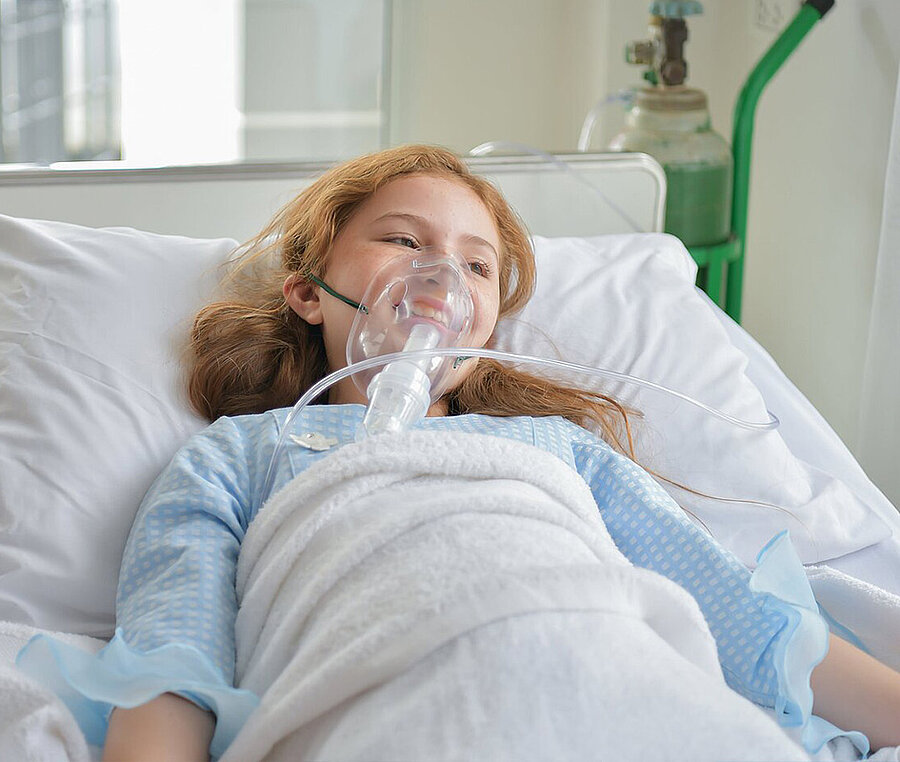
Im Rahmen seines Einsatzes für die Verbesserung des allgemeinen Wohlbefindens bietet Freudenberg innovative Lösungen für das Gesundheitswesen an. Von Luftfiltern über medizinische Schläuche bis hin zu Überwachungsgeräten für Säuglinge – unsere Produkte sind auf Sicherheit und die Verbesserung der Lebensqualität ausgelegt. Entdecken Sie, wie wir mit unseren Spitzentechnologien für das Gesundheitswesen eine gesündere Welt schaffen.
Bei Freudenberg treffen Materialkompetenz und ein Gespür für Trends in der Medizinbranche aufeinander: Expertinnen und Experten ermöglichen durch ihr Know-How die Digitalisierung medizinischer Produkte.
Beispiele dafür sind intelligente Medizinprodukte aus medizinischem Silikon, das elektronische Bauteile isoliert. Das Material kann auch als elektrisch leitende Komponenten verwendet werden kann.
Wie funktioniert das?
Elektrische Ströme werden durch die Kombination von Silikon mit leitfähigen Füllstoffen geleitet. Das erlaubt die gezielte Stimulation bestimmter Körperregionen. Die Anwendungsgebiete umfassen die Neurostimulation zur Schmerzbehandlung ebenso wie das gezielte Training von Muskelgruppen.
Silikon isoliert auch die elektronischen Komponenten und Sensoren in Medizinprodukten und schützt sie vor Schmutz, Wasser und Schweiß, damit die Geräte über einen langen Zeitraum zuverlässig funktionieren.
Überwachungsgürtel für Frühgeborene
Die zuverlässige Überwachung von Frühgeborenen ohne negative Folgen für Gesundheit oder Entwicklung stellt eine besondere medizinische Herausforderung dar. Das niederländische Start-up Bambi Medical hat den Bambi Belt entwickelt, ein innovatives Überwachungssystem für Frühgeborene. Der Bambi Belt ersetzt die Überwachung mit Klebeelektroden und Kabeln durch einen hautfreundlichen Silikongürtel.
Dieser besteht aus einer flexiblen Leiterbahn, die in verschiedene Silikone mit eingearbeiteten Sensoren eingebettet ist. Der Bambi Belt ist aus einem weichen, biokompatiblen Material gefertigt, haftet auf der Haut und lässt sich leicht ablösen. Die integrierten Sensoren erfassen die Vitalfunktionen der Frühgeborenen über die Haut. Der Gürtel ist weich und verursacht keine Schmerzen beim Anlegen oder Abnehmen. Das kabellose Design erleichtert den Eltern den Hautkontakt mit ihrem Baby. Studien belegen, dass dies die geistige und körperliche Entwicklung des Babys fördert. Freudenberg unterstützte bei der Entwicklung und Herstellung des Gürtels mit Material- und Prozesswissen.
Trainingsgerät gegen Atemaussetzer
Das Medizintechnik-Unternehmen Signifier Medical Technologies mit Sitz in London hatte das Ziel, ein Gerät zur Behandlung von Schlafapnoe zu entwickeln. Ein wesentlicher Beitrag dazu kam von Freudenberg. Gemeinsam mit Freudenberg entwickelte Signifier Medical Technologies ein neuromuskuläres Zungen-Trainingsgerät.
Das Gerät wird 20 Minuten am Tag im Mund getragen und stimuliert über eine Smartphone-App den Zungenmuskel mit minimalen Stromstößen. Das Mundstück wird bei Freudenberg in Kaiserslautern gefertigt.
Das Material für das Gerät ist elektrisch leitfähiges Silikon, das Freudenberg speziell für Signifier Medical Technologies entwickelt hat.
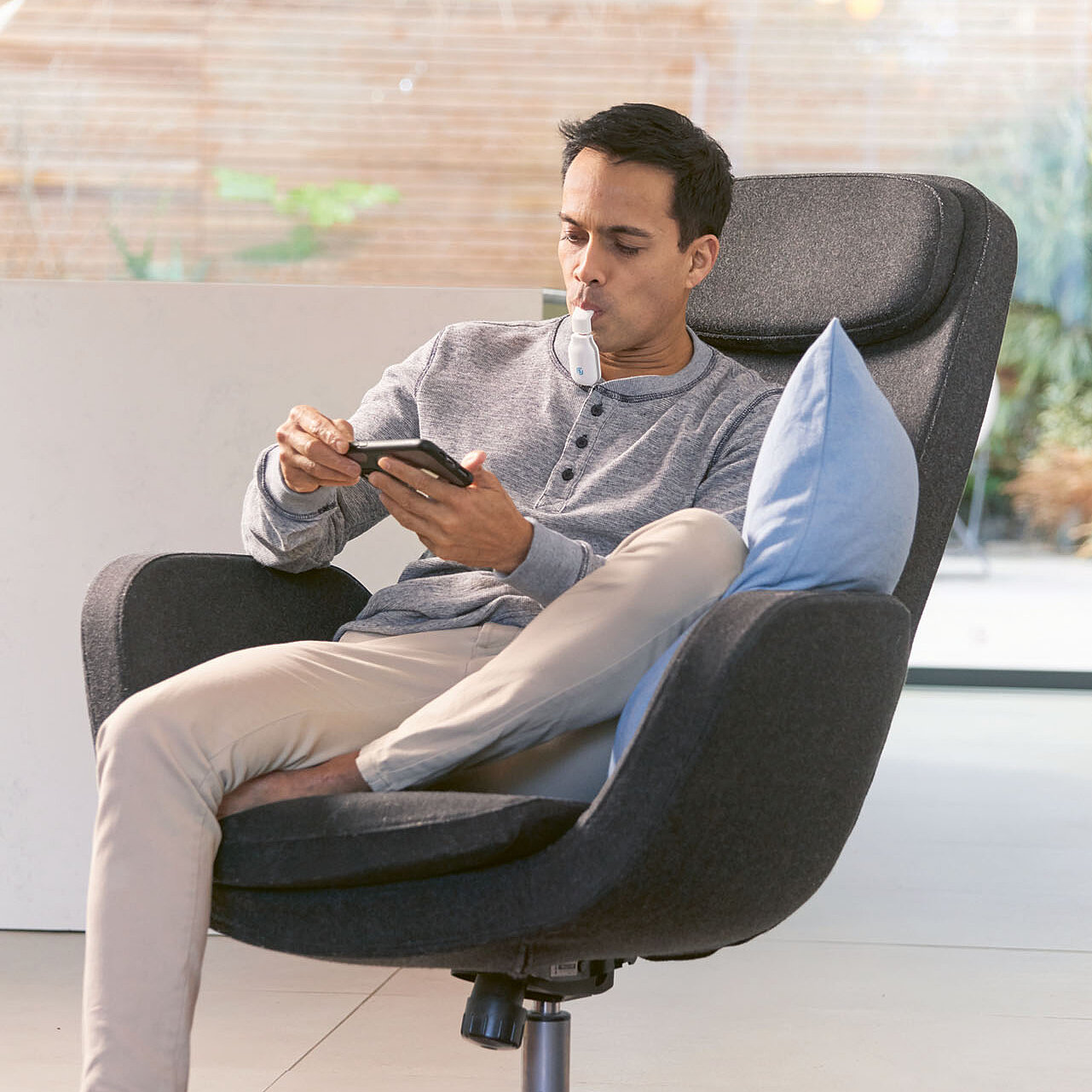
Die medizinische Entwicklung war noch nie so rasant wie heute. Da immer mehr Patienten mit modernsten Methoden behandelt werden, müssen auch die steigenden Kosten abgefedert werden. Die Trennmittel von Chem-Trend unterstützen die Hersteller von Medizinprodukten bei der Effizienzsteigerung und ermöglichen gleichzeitig Kostensenkungen sowie Qualitätsverbesserungen. Durch die enge Zusammenarbeit mit unseren Kunden bei der Überwindung der schwierigsten Herausforderungen in der Produktion spielen wir eine kleine, aber wichtige Rolle, die sowohl für die Hersteller als auch die Patienten den Ausschlag gibt.
Wir unterstützen unsere Kunden bei ihrem Streben nach nachhaltigeren Verfahren
Trennmittel von Chem-Trend spielen in vielen Fertigungsverfahren eine entscheidende Rolle, indem sie helfen, die Produktivität zu steigern, die Lebensdauer von Werkzeugen und Formen zu verlängern, die Produktion zu beschleunigen und die Ausschussrate zu senken. Durch die Steigerung der Produktivität und Wirtschaftlichkeit bieten unsere Trennmittel den Kunden auch mehr Nachhaltigkeit in der Fertigung.
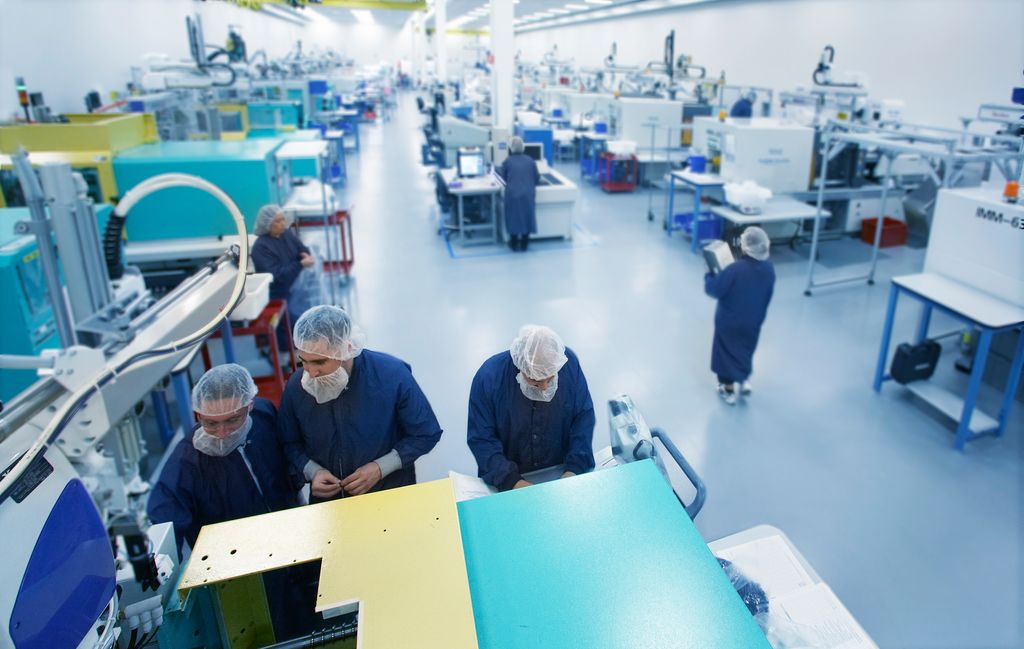
Unsere enge Zusammenarbeit mit dem medizintechnischen Bereich und anderen Branchen bringt maßgeschneiderte Innovationen zur Verbesserung der Produktionsverfahren hervor.
Seit der Entwicklung des ersten wasserbasierten Formtrennmittels durch Chem-Trend in den 1960er Jahren haben wir umfangreiche Ressourcen in die kontinuierliche Innovation investiert. Als weltweit führender Anbieter von Trennmittelsystemen und -lösungen sind wir stolz auf unsere Rolle als vertrauenswürdiger Partner für die Hersteller in einer Vielzahl von Branchen.
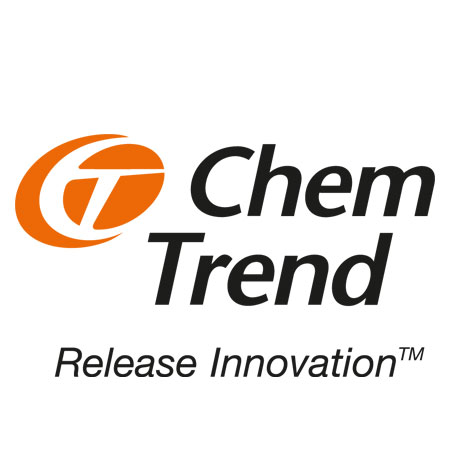