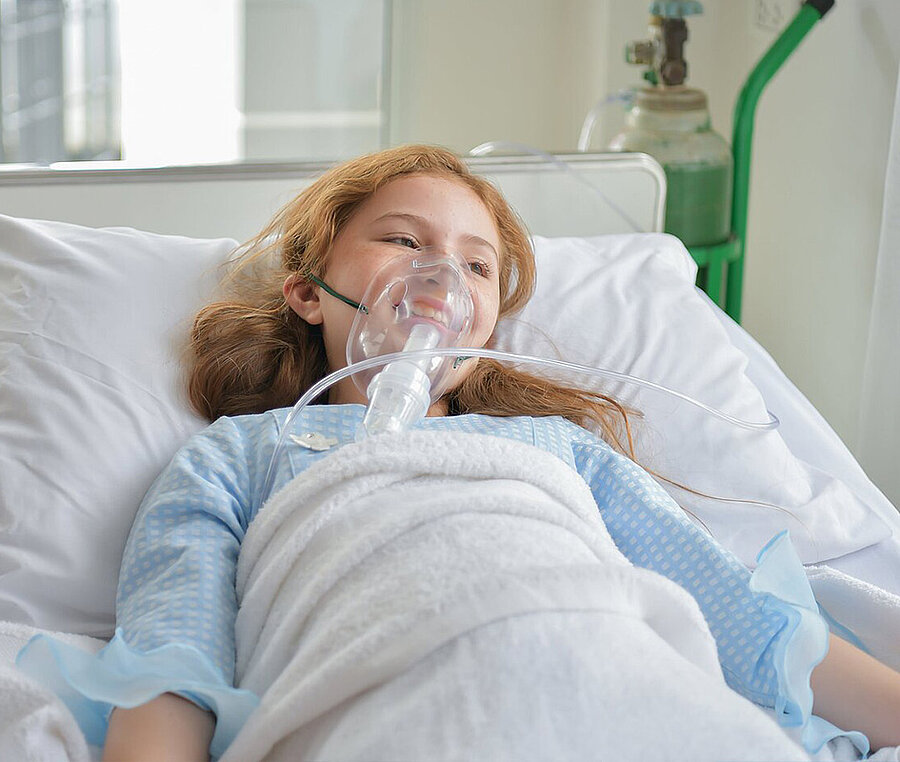
Innovations for better lives
How we transform healthcare with cutting-edge technology
Committed to enhancing overall well-being, Freudenberg offers innovative healthcare solutions. From air filters to medical tubing to infant monitoring devices, our products are designed to ensure safety and improve lives. Discover how we are creating a healthier environment with our cutting-edge healthcare technologies.
Digital technologies for the healthcare of the future
Freudenberg combines expertise in materials with a feel for trends in the medical industry. Our experts at Freudenberg Medical are using their know-how to bring digitalization to medical devices.
Some examples of these are intelligent medical devices made from biocompatible silicone, which insulates electronic components. This material can also be used as an electrically conductive component in medical devices.
How does this work?
Electrical currents are conducted by combining silicone with conductive fillers. This allows specific areas of the body to be stimulated in a targeted manner. Areas of application include neurostimulation for pain treatment or the targeted training of muscle groups.
Silicone also insulates the electronic components and sensors in medical devices, protecting them from dirt, water and sweat so the devices can operate reliably for a long time.
Monitoring belts for premature babies
Reliable monitoring of premature babies without impairing their health or development is a particular medical challenge. The Dutch start-up Bambi Medical has developed the Bambi Belt, an innovative monitoring system for premature babies. The Bambi Belt replaces monitoring with sticky electrodes and cables with a skin-friendly silicone belt.
It consists of a flexible conductor track embedded in various silicones with integrated sensors. The Bambi Belt made from a soft and biocompatible material, adheres to the skin and is easy to remove. Integrated sensors record the premature baby’s vital functions via the skin. The belt is soft and can be put on and taken off without causing any pain. Thanks to the wireless design, parents can easily make skin-to-skin contact with their babies. Studies prove that this promotes the baby’s mental and physical development. Freudenberg’s expertise in materials and processes was a key contribution to the belt’s development and manufacture.
Training device against apnea
The London-based medical technology company Signifier Medical Technologies had the goal of developing a device to treat sleep apnea. Freudenberg made a significant contribution to this. Together with Freudenberg, Signifier Medical Technologies developed a neuromuscular tongue training device.
The device is worn in the mouth for 20 minutes a day and stimulates the tongue muscle with minimal electric shocks, controlled via a smartphone app. The mouthpiece is manufactured by Freudenberg in Kaiserslautern.
The material used in the device is an electrically conductive silicone that Freudenberg developed especially for Signifier Medical Technologies.
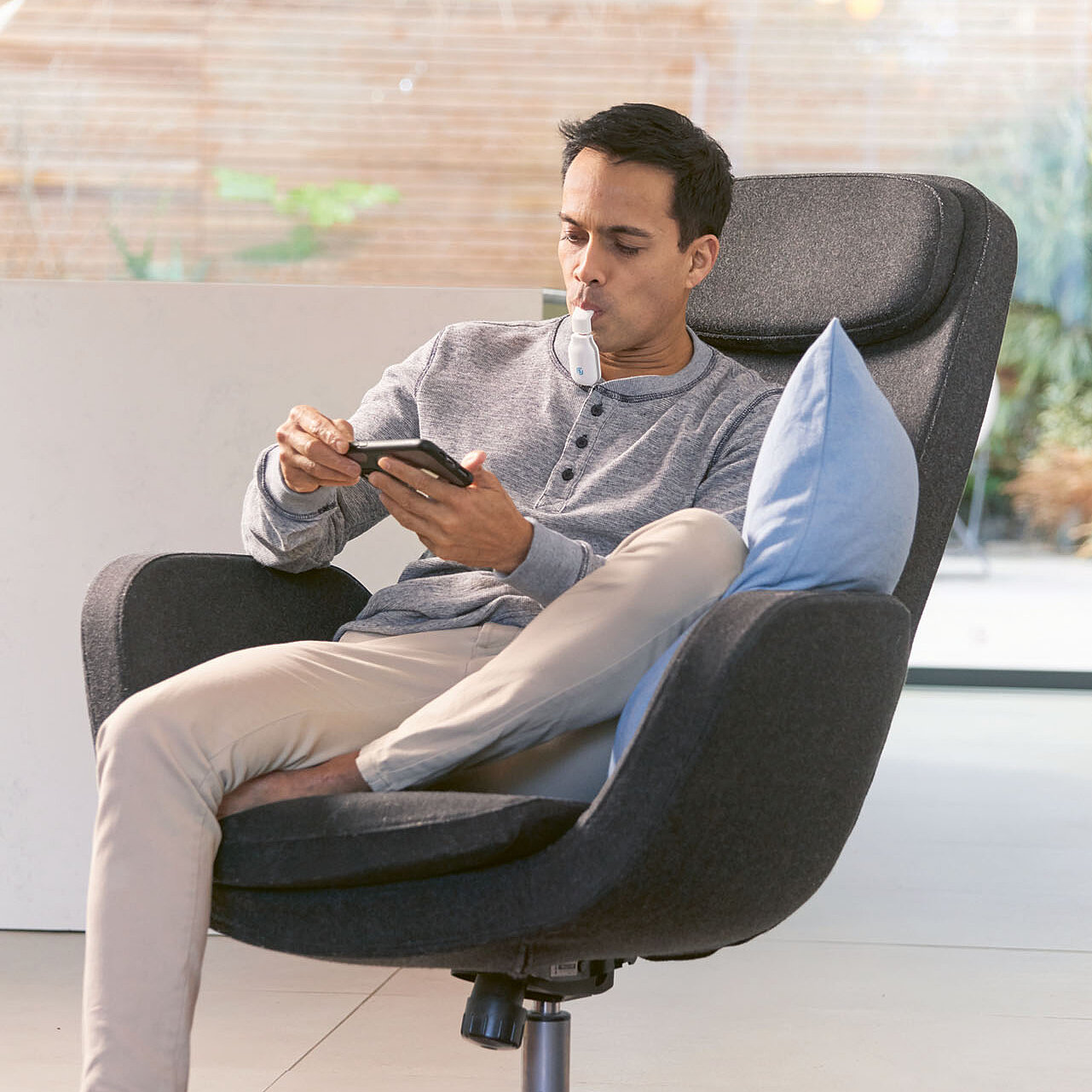
biocompatible release agents boost efficiency & improve quality
Medical development has never progressed so fast. With more and more patients receiving cutting-edge care, the rising expenses must be countered. Chem-Trend’s release agents help manufacturers of medical equipment boost efficiency, generate lower expenses, and improve quality. Collaborating closely with customers to solve the most difficult production challenges, Chem-Trend plays a vital role - one that makes a difference to manufacturers and patients alike.
We help our customers to make their operations more sustainable
Chem-Trend release agents play a vital role in many manufacturing processes - helping to enhance productivity, prolong the lifespan of tools and molds, accelerate production, and reduce defect rates. Thereby they do not only increase productivity and profitability, but our technology also helps manufacturers to make their production more sustainable.
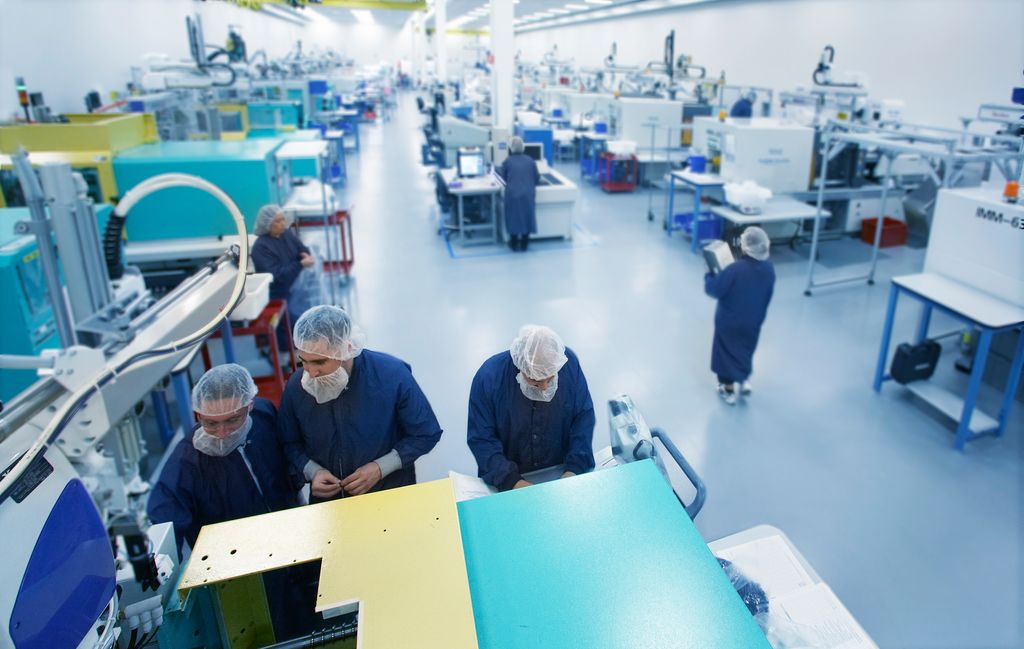
Our close collaboration with the medical sector and other industries leads to custom-made innovations that improve manufacturing production at a variety of levels.
Since Chem-Trend developed the first water-based die lubricant in the 1960s, the company has invested extensive resources to continuously innovate and become a world leader in release agent systems and solutions and a trusted partner for manufacturers in a broad range of industries.
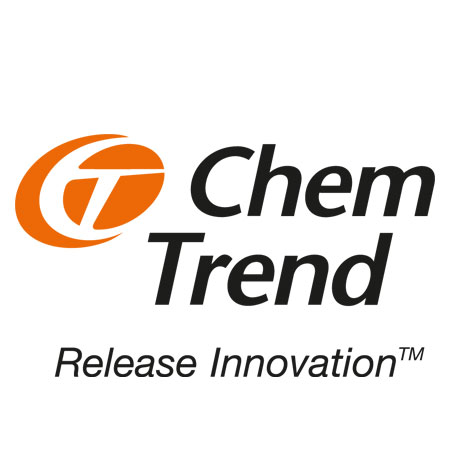