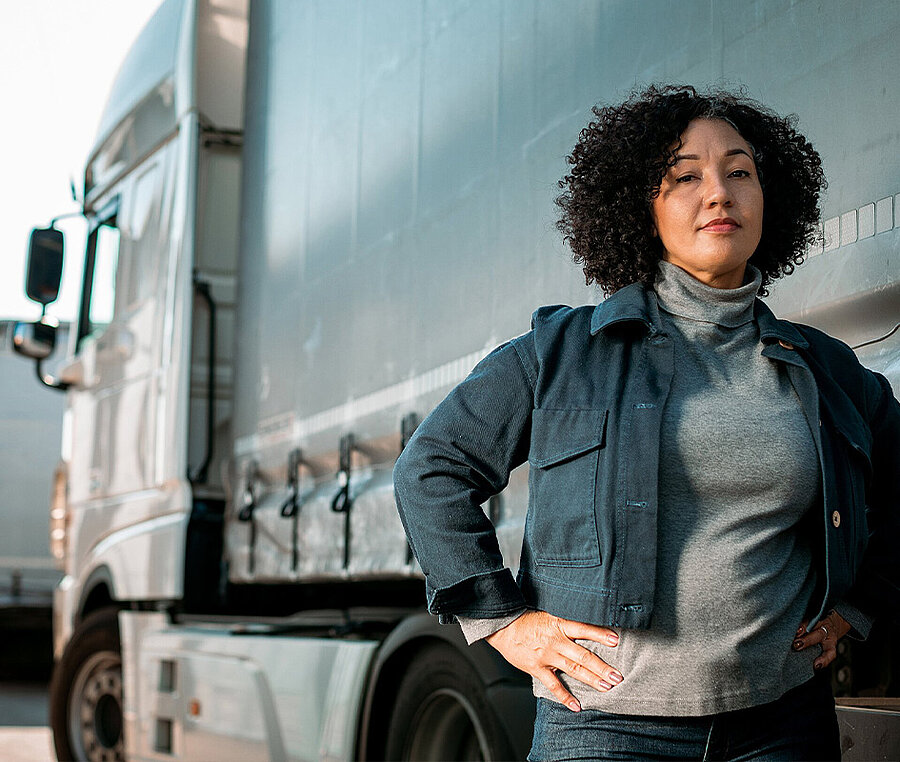
INNOVATIVE MOBILITY SOLUTIONS FOR A DYNAMIC WORLD
How we enable sustainable mobility
Driven by innovation, Freudenberg is transforming the way people move with our cutting-edge smart mobility solutions. From electric vehicles to intelligent transportation systems, our innovations are designed to make travel safer, more efficient, and environmentally friendly. Discover how we are revolutionizing mobility for a smarter future.
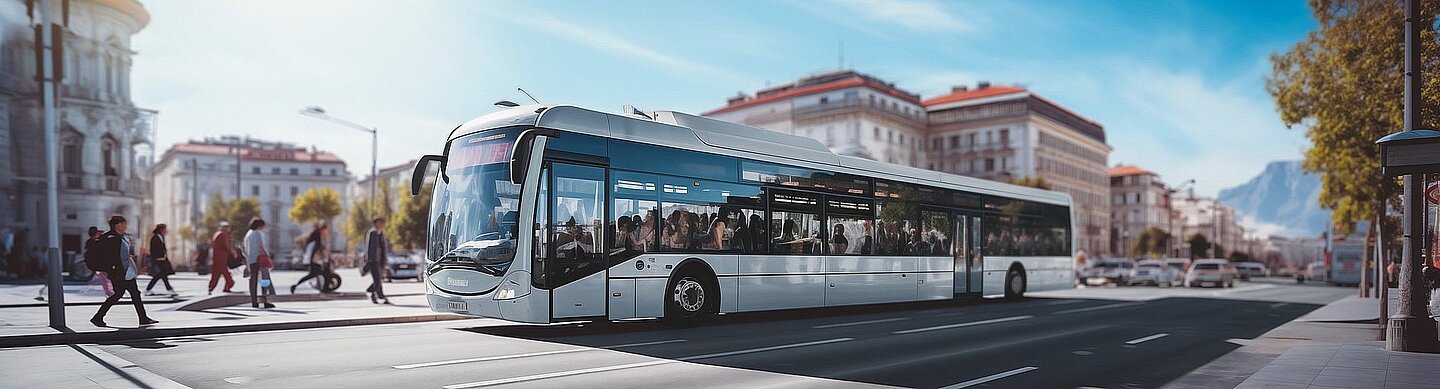
E-mobility: safe, efficient and durable
Freudenberg is combining material expertise and innovation to make electric mobility safe and durable.
Improvements in performance are another goal. We offer vehicle makers a broad portfolio of solutions, ranging from battery systems to high-performance materials and even efficient pressure management technologies. Freudenberg’s Business Groups are drawing on their decades of experience and their in-depth technical know-how as they actively support the mobility transformation.
Optimized solutions for heavy-duty applications
To meet the growing demands in the heavy-duty sector, Freudenberg has taken its know-how in the battery and fuel cell fields and bundled it into a special Business Group: Freudenberg e-Power Systems.
As a provider of emission-neutral energy systems, Freudenberg e-Power Systems develops innovative solutions for the challenging heavy-duty sector. Our battery and fuel cell systems are specifically designed and customized for buses, trucks, maritime and off-road applications to provide our customers with optimal, safe solutions for every application. Robust housings, precise thermal management, and smart monitoring systems are delivering reliable performance - even under extreme loads.
Protection against extreme temperatures
Even beyond heavy-duty applications, Freudenberg is turning to innovative solutions to make battery systems in electric vehicles safer while boosting their performance. Here highly sophisticated materials play a key role.
One example is Quantix® ULTRA. It provides reliable flame protection and limits the spread of potential flames within the battery module. Especially in conductor rails, also known as busbars, the high-performance material decreases the risk of short circuits and helps to regulate temperatures efficiently.
The heat shield provides additional protection. It is a silicone-based elastomer with a waffle-like structure. This protective thermal layer keeps high temperatures from reaching adjacent battery modules.
Special Freudenberg materials also function as thermal barriers in battery compartments. They withstand temperatures of up to 1,200°C and prevent the uncontrollable release of the tiny particles that are produced when a cell is defective.
We have succeeded in combining the worlds of thermoplastics and thermosets.
Dr. Björn Hellbach
Senior Chemical Specialist at Freudenberg Sealing Technologies
Efficient pressure management
Aside from thermal protection, thermal management plays a significant role in promoting a long operating life for battery systems. The innovative venting system DIAvent® provides safe pressure equalization within the battery module. During normal operation, a “breathing” membrane enables controlled air exchanges while keeping water and dirt from penetrating. In case of a critical battery event, DIAvent® opens up instantly, draining off gases safely and preventing a dangerous pressure increase.
Protection against exposure to fluids
Protection against exposure to fluids is another important factor affecting the lifespan of a battery system. Humidity or a leaking coolant can damage sensitive electronics and cell modules. Freudenberg's Battery Pack Liquid Absorbers effectively absorb and store any liquid that may appear, preventing potential damage to the system.
How Freudenberg is driving change for the better
As a pioneer in the field of e-mobility, Freudenberg e-Power Systems is at the forefront of bringing emission-free solutions to the road and to the ocean - providing answers to the questions of a sustainable future.
Battery and fuel cell systems are offering impactful solutions when it comes to lowering emissions for mobility and logistics. Freudenberg’s e-mobility solutions have been developed with more than 25 years of experience to meet the needs of the industries as well as driving a more sustainable future. Powerful, reliable and cost-efficient, Freudenberg’s systems provide carbon neutral solutions for the commercial vehicle industries.
With customized solutions for the maritime industries, Freudenberg provides even cruise ships with zero-emission solutions.
We are committed to provide energy systems that maximize efficiency, durability and lower the total costs to shape the future.
With its dedicated experts, strong focus on innovation and pioneering mindset, Freudenberg e-Power Systems combines deep technical knowledge with the power to industrialize battery and fuel cell systems at scale to realize industry tailored solutions.
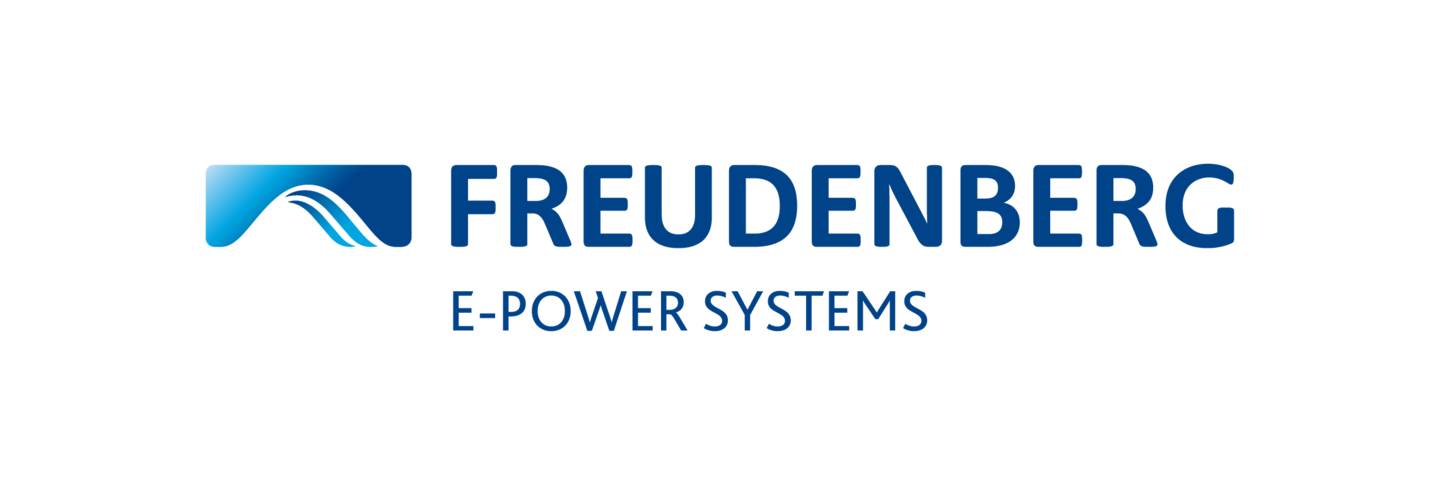