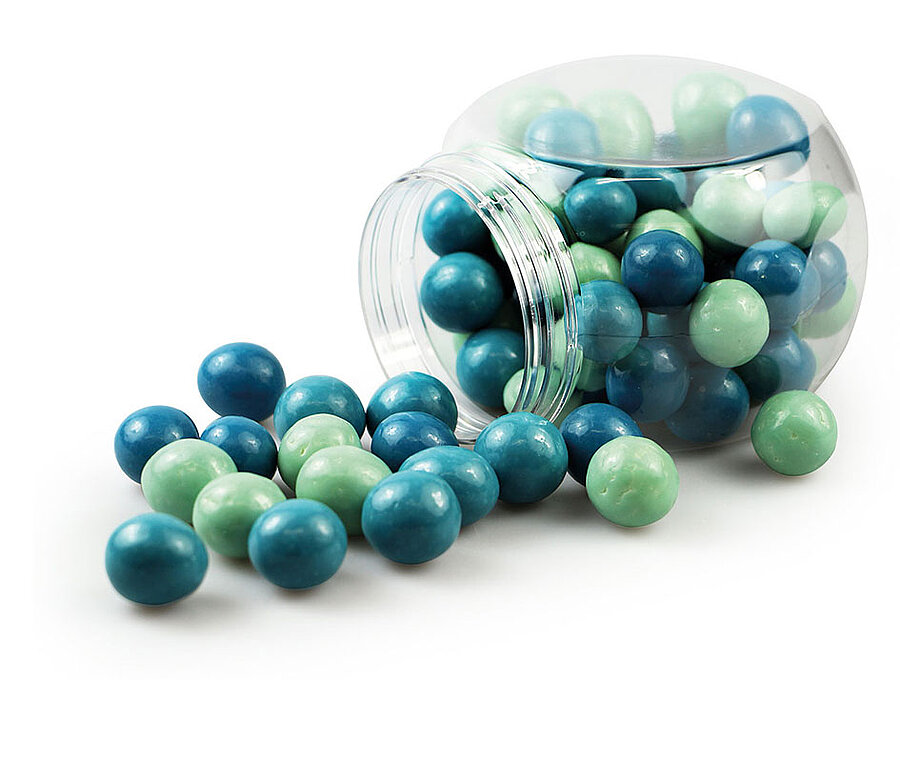
Enhancing quality in food & Beverage
How we support with natural alternatives
At Freudenberg, we enhance the quality and safety of food production through innovative solutions. From enhancing the surface of sweets to providing advanced lubrication for food production machines, our technologies guarantee efficient and safe processes. Discover how we are promoting a healthier future by supporting the food and beverage industry.
Sweet sustainability: Confectionary surface treatment And natural colors
Who can resist shiny chocolate or jewel-colored candy? It’s good to know the color and shine provided by CAPOL, a Freudenberg company, is derived naturally and sustainably.
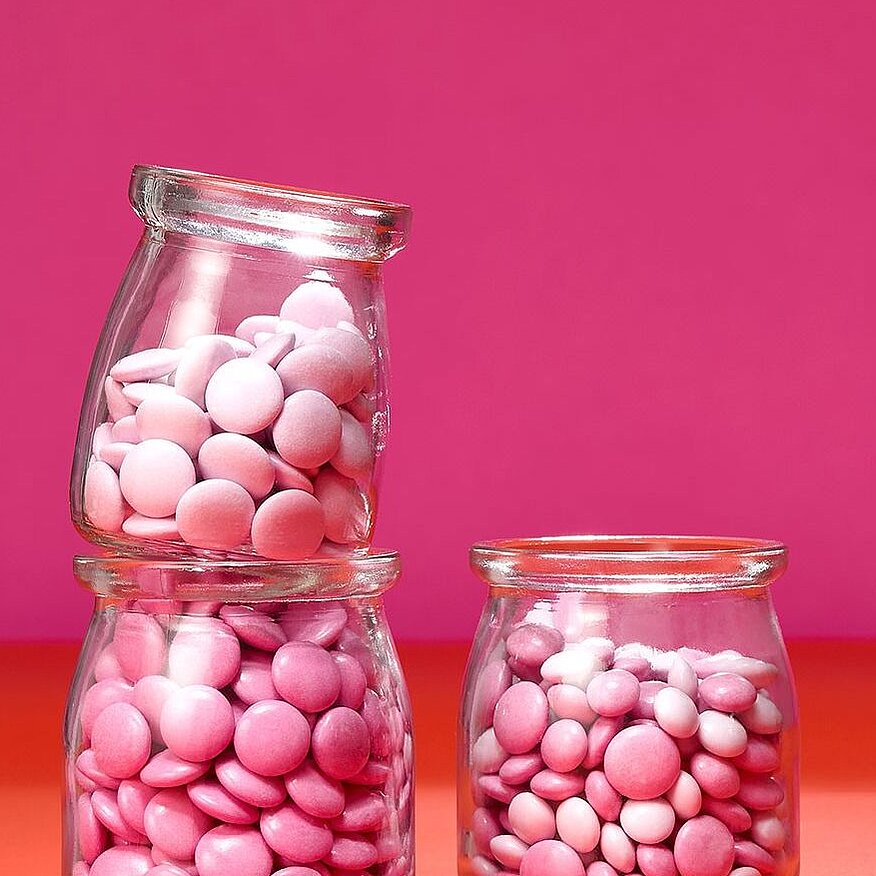
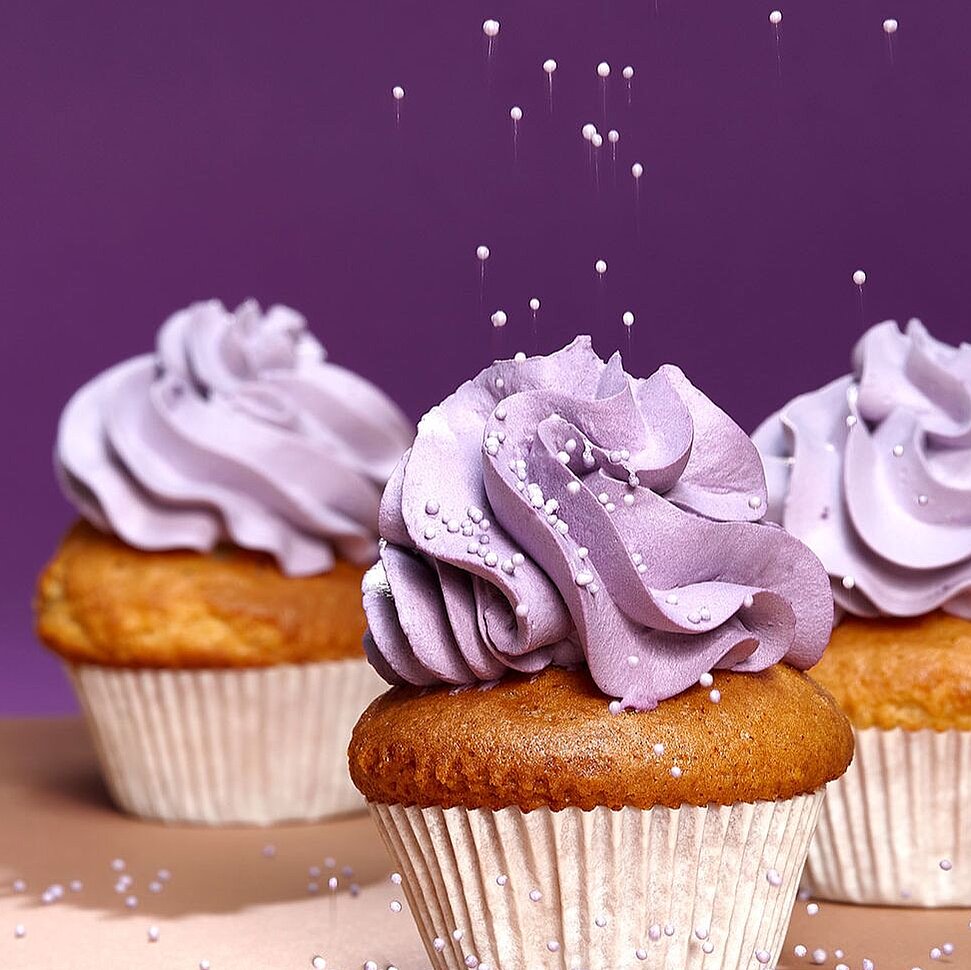
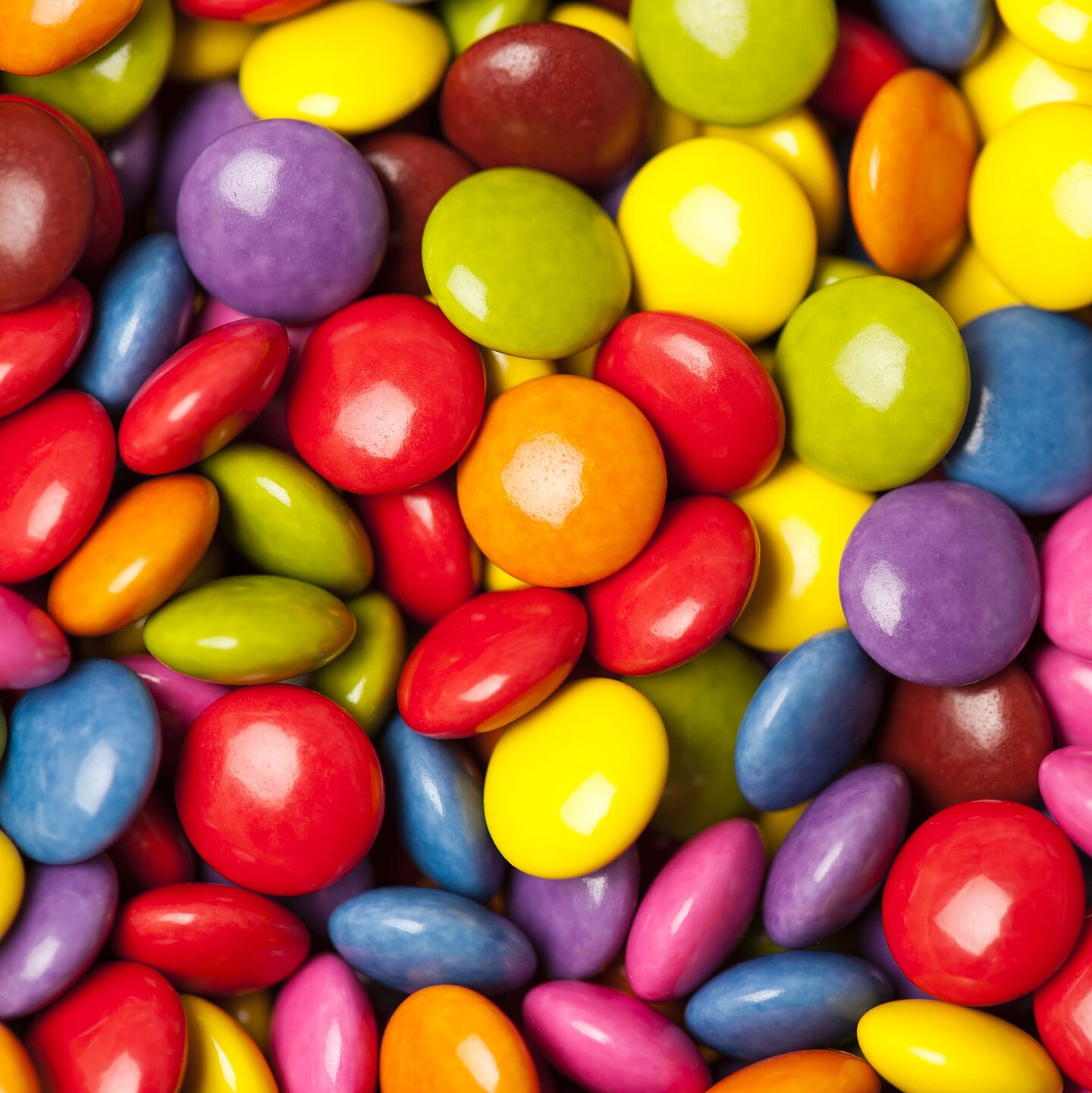
Customers have developed a demand for quality, transparency, and sustainability with their food
The confectionary industry is experiencing a change in customers' needs: Consumers are adopting a more mindful approach to sweets, paying attention not only to the sugar intake but also the additives used.
Vegetarians and vegans are rejecting the use of animal-derived ingredients. Additionally, there is a growing awareness of how food affects the planet as well as health and wellness. Consumers are becoming increasingly conscious about artificial additives. These lifestyle changes are driving a significant shift in the industry to meet the consumers' ethical and dietary needs.
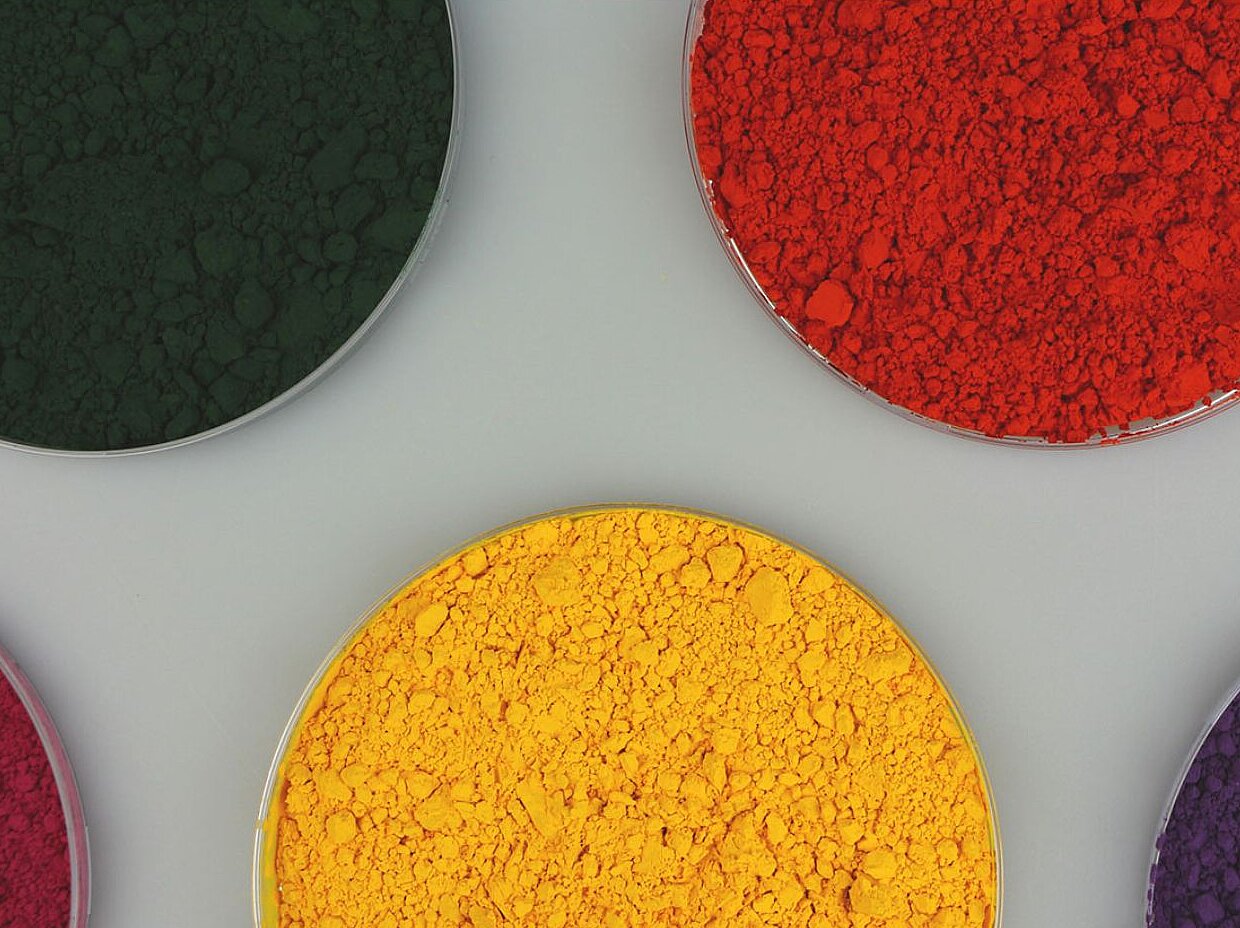
Experience and innovation: Natural colors by CAPOL
CAPOL’s natural color pigments are based on natural sources like fruit and vegetables, making synthetic colors obsolete. A leading technology preserves the vibrant colors from natural sources and turns them into pigments that serve various applications throughout the confectionery and food categories.
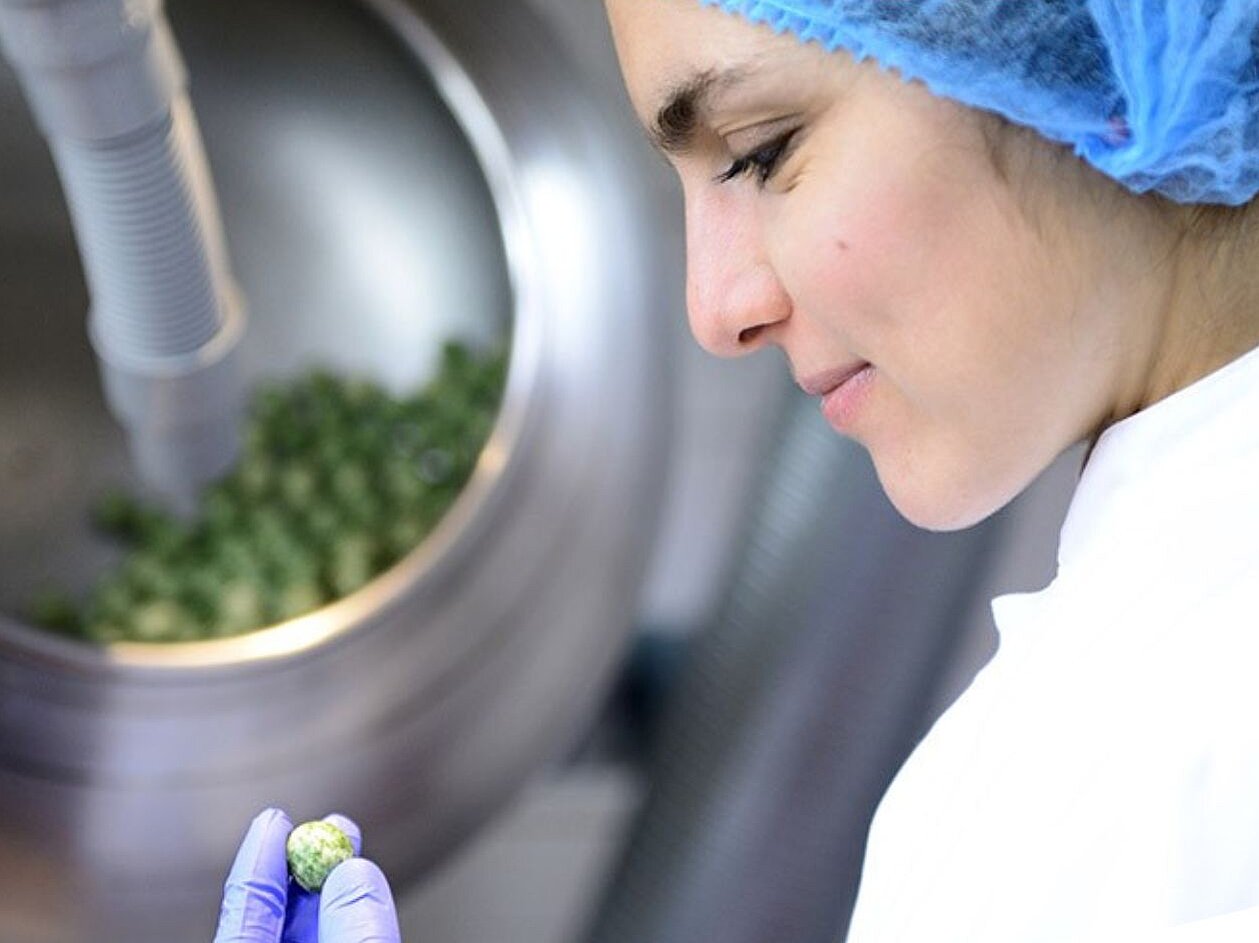
Founded in 1975, CAPOL has provided over 250 made-to-measure color and coating solutions to manufacturers in more than 100 countries worldwide. Globally expanded, the company joined the Freudenberg Group in 2013. More than a decade ago, Capol became the first company in the confectionary industry to use certified sustainable raw materials and offer RSPO certified (MB) products.
.
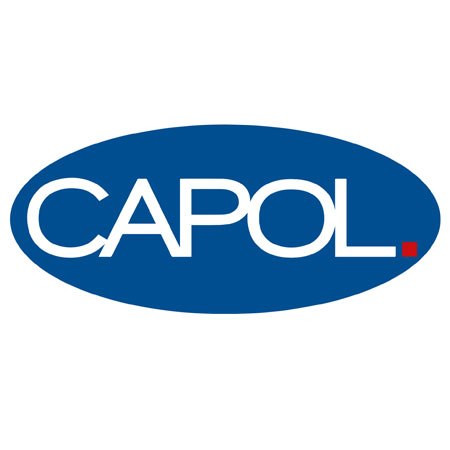
Modern technology meets tradition: Glenmorangie & Aquabio
Glenmorangie’s whiskeys are enjoyed worldwide, but according to its founders, it can only be crafted in one place – the town of Tain in the northeast of Scotland. To preserve this unique heritage for future generations, they partnered with Aquabio, a Freudenberg company, to protect the environment. Now, the by-products of distillation are converted into energy and fertilizer. The water used is filtered to 95% allowing the marine ecosystem to recover. Wastewater is truly becoming “the water of life” once again.
Filtration solutions by Aquabio help the environment heal
Glenmorangie had an ambitious plan: to save the environment that does so much for them and their whisky. They wanted to improve the water quality and biodiversity in the nearby sea by setting up oyster banks, healing the ecosystem after decades of overfishing.
Aquabio, a Freudenberg company, developed the solution: They provided the anaerobic membrane bioreactor. A low energy solution that uses bacteria to digest the distillery’s waste into valuable fuel, fertilizer and then filter water to be given back to nature without any risk to the environment.
How the modern Aquabio filtration solution works:
The by-products of the distillery are made into
- biogas to cut the company’s fossil fuel consumption by 15%
- a nutrient-rich fertilizer, rich in copper, to grow the region’s barley
- water that is 95% free of organic compounds
This system is modular and can easily be adapted by other industries to benefit by making waste into resources and improving the environment.