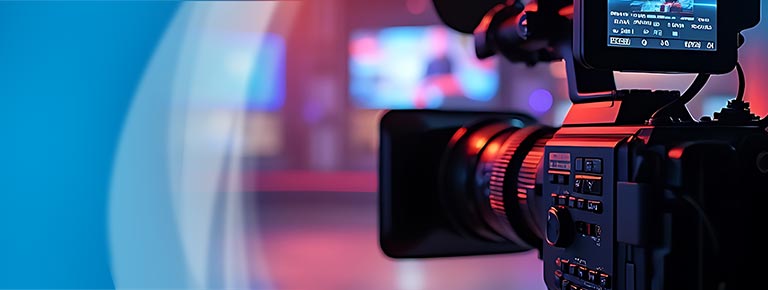
Press & Media
Welcome to the Freudenberg press & media center
Get the latest news with our press releases, photos and footage, publications as well as our social media posts.
Contacts
Freudenberg & Co. KG
Hoehnerweg 2-4
69469 Weinheim
Germany
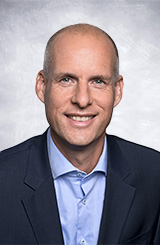
Freudenberg & Co. KG
Hoehnerweg 2-4
69469 Weinheim
Germany
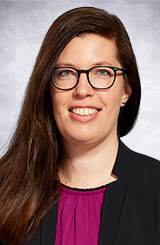
Freudenberg & Co. KG
Hoehnerweg 2-4
69469 Weinheim
Germany

Our press releases
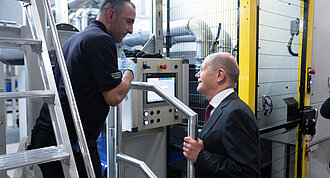